Hopfendrahtaufhängung
Unter Berücksichtigung der Tatsache, dass die Befestigung der Aufleitdrähte als manuelle Arbeit mit erheblichem Unfallrisiko eingestuft werden muss, dass die Arbeit unter schweren Witterungsbedingungen durchgeführt wird und ergonomisch betrachtet sehr belastend ist, muss eine Automatisierung angestrebt werden.
Zielsetzung
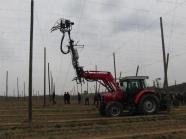
Hopfendrahtbinder Feldeinsatz
Methode
In der ersten Phase des Projekts wurden die bestehenden technischen Zeichnungen der Einzelteile überarbeitet und in 3D-Volumenmodelle konvertiert. Alle neu konstruierten oder optimierten Einzelteile wurden als 3D-Volumenmodelle erzeugt. Auf diese Weise wurde die durchgängige Bearbeitung der gesamten Prozesskette vom Entwurf bis zur Fertigung eines zweiten Prototyps möglich.
In einer weiteren Phase des Projekts wurden die Prozessparameter (hydraulischer Druck, Durchfluss und Temperatur an den Hauptölleitungen) am ersten Prototyp unter realen Bedingungen während einer Vielzahl von Bindevorgängen ermittelt und analysiert. Die Messungen wurden mit einer kompakten modularen Messplattform durchgeführt, wozu eine angepasste Softwarelösung entwickelt wurde.
Parallel wurde das Subsystem zur Drahtzwischenspeicherung unter Laborbedingungen analysiert und optimiert.
Mechatronisches System zur vollautomatischen Drahtaufhängung im Hopfenanbau
Projekthintergrund und Motivation
- Anbaufläche in Deutschland 18.500 ha, davon 15.500 ha in Bayern
- Überwiegend 7 - 8 m hohe Gerüstsysteme
- Jährliche Erneuerung der Aufleitdrähte (Stahldraht mit 1,2 – 1,4 mm Durchmesser)
- Manuelle Befestigung der Aufleitdrähte:
- 3 Mann-Kanzel 12 Arbeitskraftstunden (Akh) und 3 Schlepperstunden (Sh) pro ha
- 2 Mann-Kanzel 15 Akh und 5 Sh pro ha
- Probleme bei der manuellen Befestigung:
- Hohes Unfallrisiko
- Ergonomie (hohe Arbeitsbelastung)
- Witterungsabhängigkeit
Ergebnisse
- Flächenleistung zwischen 0,21 und 0,23 ha/h
- Durchschnittliche Arbeitsgeschwindigkeit zwischen 1,45 und 1,65 km/h
- Umfangreiche Erprobungen werden in der Saison 2011/12 fortgesetzt
Aktivierung erforderlich
Durch das Klicken auf diesen Text werden in Zukunft YouTube-Videos im gesamten Internetauftritt eingeblendet.Aus Datenschutzgründen weisen wir darauf hin, dass nach der dauerhaften Aktivierung Daten an YouTube übermittelt werden.
Auf unserer Seite zum Datenschutz erhalten Sie weitere Informationen und können diese Aktivierung wieder rückgängig machen.
Der Film stellt parallel die Simulation eines Drahtbindevorgangs mithilfe eines digitalen 3D-Modells des Bindekopfs und die Erprobung des Geräts unter realen Bedingungen dar. Die Erprobung ist aus zwei Perspektiven geschildert: zum einen ist der Drahtbindekopf detailliert und zum anderen die Bewegung des Geräts im Hopfengarten während des Einsatzes dargestellt. Die Erprobung des Gerätes zeigt sowohl das Anbinden der Aufleitdrähte, als auch die automatisierte Antastbewegung des Bindekopfes an den Spanndraht und die Ausweichbewegung beim Passieren der Querdrähte. In der Gesamtdarstellung der Bewegung des Gerätes im Hopfengarten kann auch die Wirkungsweise des Drahtspeichers erkannt werden.
Ergebnisse
Der virtuelle 3D Prototyp ermöglichte sowohl ein detailliertes Modellieren aller Bauteile und ihren virtuellen Zusammenbau zu Baugruppen als auch die Durchführung von kinematischen Analysen.
Die Entwicklung des virtuellen Prototyps war die Grundlage für die weitere Optimierung des dynamisch betrachtet sehr komplexen Subsystems „Bindekopf“. Im Gegensatz zum ersten Prototyp wurden für das Aufstellen des Bindekopfs und das Biegen des Aufleitdrahts um den Spanndraht des Hopfengerüsts herum statt einfachwirkender Zylinder zwei Schwenkmotoren mit Endlagedämpfung eingebaut. Die Bewegungsabläufe des Subsystems wurden simuliert und analysiert. Basierend auf den Ergebnissen wurden die Einzelteile optimiert. Mögliche Konstruktionsfehler wurden durch die Analyse mit dem virtuellen Prototyp minimiert und die Entwicklungszeit deutlich verkürzt.
Bei der Beobachtung der Prozessparameter des ersten Prototyps wurden die Ausführungszeiten der vier zeitkritischsten Vorgänge analysiert, ausgewertet und ihre Abweichung vom theoretischen Sollwert diskutiert. Als Ursache für die Schwankungen der Ausführungszeiten wurde Schlupf am Drahttransportsystem identifiziert und durch die Erhöhung der Reibung zwischen Draht und Vorschub- bzw. Nachfüllmechanismus reduziert. Diese Änderung bewirkte aber einen erhöhten Leistungsbedarf und verlangte eine konstant zur Verfügung stehende Hydraulikleistung. Um diese zur Verfügung zu stellen und um Leistungsschwankungen in beiden Mechanismen zu vermeiden, wurde eine Konzeptänderung erarbeitet, bei der das Hydrauliksystem in zwei unabhängige Hydraulikkreise aufgeteilt wurde. Ein Hydraulikkreis versorgt die Turmsteuerung und den Drahtspeicher, der zweite Hydraulikkreis alle Operationen der Drahtbindung und des Vorschubes.
Der Drahtzwischenspeicher, eine Vorrichtung zwischen dem Bindekopf und der Drahtvorratsrolle zur Erhöhung der Vorschubgeschwindigkeit des Drahtes, wurde optimiert, damit sich der Aufleitdraht beim schnellen Abziehen von der Vorratsrolle nicht verknotet oder verhakt. Im Rahmen der Optimierung wurde die Wirkung des Antriebsmotors vom Mechanismus, der den Drahtzwischenspeicher rechtzeitig auffüllen soll, untersucht. Um den Drahtzwischenspeicher rechtzeitig aufzufüllen, ohne dass sich der Draht im Bereich zwischen Drahtvorratsrolle und Drahtspeicher verhakt, wurden zwei Auffüllgeschwindigkeiten definiert, wobei eine Reduzierung am Anfang und am Ende des Auffüllzyklus aktiviert wird.
Die Steuerung des Hopfendrahtbindegeräts wurde mit einer SPS der Fa. Mitsubishi Electric und durch Kooperation bei der Programmierung mit dem Hersteller realisiert. Neben dem vollautomatischen Betrieb lässt sich über eine Fernbedienung die Position des Geräts korrigieren und der Ablauf des Bindevorgangs manuell steuern.
Der auf diese Weise realisierte zweite Prototyp des Geräts zur automatischen Aufhängung von Aufleitdrähten wird im ersten Quartal 2010 intensiv getestet, um die Funktionalität aller optimierten Teilsysteme zu prüfen und eventuelle Mängel beseitigen zu können.
Projektinformation
Projektleitung Dr. Zoltan Gobor (Gesamtprojekt: J. Portner, LfL IPZ 5a)
Projektbearbeitung Th. Kammerloher, Dr. G. Fröhlich, Werkstatt
Laufzeit 2008-2010
Projektpartner Soller GmbH, IPZ 5
Finanzierung BLE
Entwicklung und Optimierung einer Maschine zur automatischen Hopfenpflücke
Trotz der Bedeutung des Hopfenanbaus blieb der technische Fortschritt in der Produktion hinter den technischen Entwicklungen auf dem Agrarsektor zurück. Das manuelle Einhängen der Hopfenreben in die Pflückmaschine ist eine anstrengende, ergonomisch belastende und unfallträchtige Tätigkeit. Mehr